

ABOUT US
PROXIMITY, AGILITY & FLEXIBILITY
That’s what makes the difference, and why our solutions are so many times the first choice.
We are a global company but keep the best that a family-owned business can have: agility in developing new products, a flexible production and the proximity to our staff and clients.
History
We began in 1983 as a steam specialist contractor. A few years later we started developing products for industrial steam and fluid systems and since then we never stopped growing.
-
Due to the financial instability of some companies after the April Revolution in 1974, the young technician Fernando Pereira Rodrigues Soares took the opportunity to establish his own company with three other business partners. Even though the main activity was the assembly of steam systems, compressed air and thermal oil systems it was during this period that Mr. Soares designed equipment which are still being manufactured today, namely humidity separators and heat exchangers.
-
First floating head heat exchanger.
-
Mr. Soares formed his first family business named Eurofluido. Initially, he dedicated himself to the design and construction of humidity separators, heat exchangers, reservoirs and other parts of machinery, as well as their assembly and sale. He also imported steam traps, pressure reducing valves and other accessories, which were incorporated into installations or resold.
-
First condensate recovery unit.
-
First shell & tube heat exchanger.
-
The brand named ADCA - Mrs. Adozinda Cachulo’s initials - was registered and the first steam traps and ADCAMat pressure operated pumps were designed.
-
First time a manufactured equipment with the ADCA brand was exported.
-
Launch of the first ADCA pressure regulators.
-
The first factory was built in Sintra, Lisbon, centralizing all fields of activity. Serial production was developed with automated equipment and subcontracted CNC machinery.
-
The company decided to concentrate its efforts solely in its most promising activity: Manufacturing. To this end, a company founded in 1991 was re-established under the name of Valsteam Engineering SA. The core business was the engineering and manufacturing of steam equipment and fluid network components. The headquarters were located in Lisbon and the factory in Leiria. In order to finance these operations, the family’s assets were sold.
-
Valsteam Engineering SA became the equipment manufacturer it is known as today. It completely ceased its assembly and re-sale activities of equipment produced by other manufacturers. The company became self-sufficient in manufacturing, finishing and welding operations.
-
The company’s quality system was certified under the ISO NP EN 9001 standards.
-
The company’s name was changed to Valsteam Adca Engineering S.A. and it incorporated the brand ADCA, which was already known in the international market. The field of metallic construction gained strength with the re-introduction of heat exchangers to the company’s portfolio.
-
This activity was transferred to a nearby rented warehouse (1800 m2) and the manufacturing procedures were improved.
-
The UNIAdca range was introduced and the ADCATrol control valve project began.
-
The company welcomed the first member of the second generation.
-
Two big facts in the same year: ADCAPure brand was launched and another member of the second generation started working at Valsteam.
-
A big step. Beginning of the construction of a new factory with a total area of 22.000m2. In the middle of the year, the second phase of construction began, allowing incorporation of the welding department with space to install more new machinery.
-
The year started with all the company sectors already established in the new facilities.
-
The construction of a new factory (Building 2) dedicated to metallic construction with a further 2.650m2 of space dedicated to all associated processes such as welding, testing and assembly of skids.
-
With the completion of the construction of Building 2, a new structural reorganization took place. CNC machinery was transferred to the space previously occupied by the mechanical construction department in Building 1 allowing space for the introduction of new machinery.
-
Time to welcome the third member of the second generation.
-
Beginning and finishing a new advanced 329 m2 test bench.
-
Beginning of the construction of a new expansion of 7.000m2, duplicating the production area.
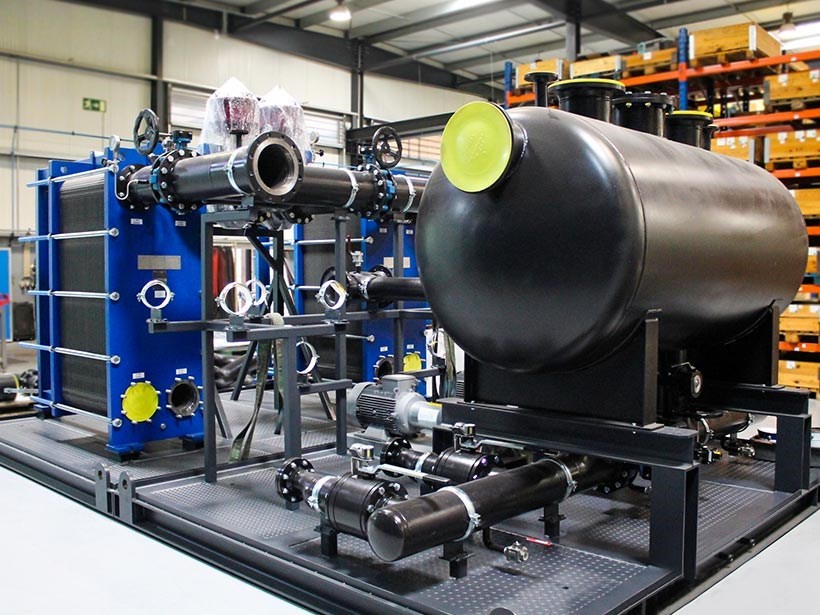
Technology
As a “one-stop-shop” and a full-service manufacturer, we assure the complete production cycle: design, machining, welding, assembly, tests, quality, and packaging. A complex system that depends on the high technology we use.
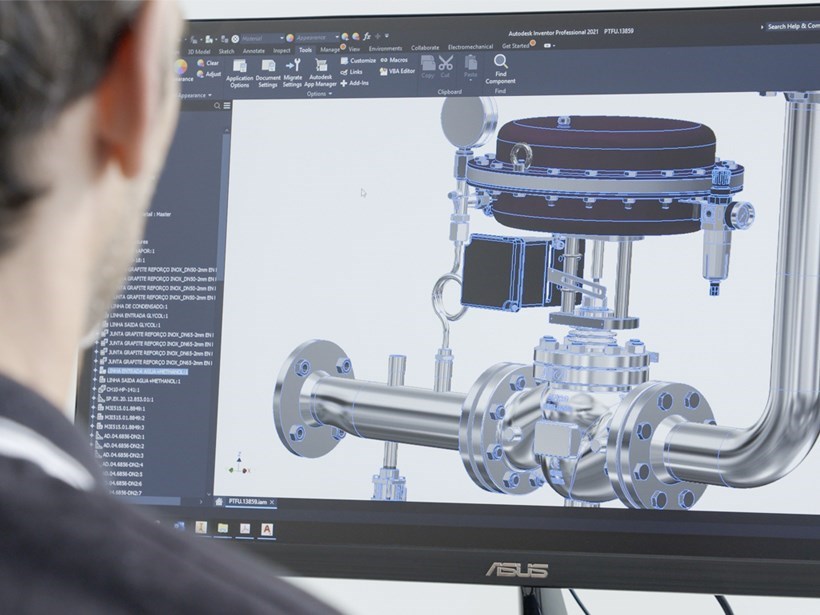
Technology
R & D
We are innovators by nature, always researching and developing effective solutions and products. The development of our products begins in our design and engineering departments, where out teams of designers and engineers use advanced engineering software and acquired knowhow.

Technology
Welding
Several welding procedures such as orbital, manual and mechanized TIG, MMA (stick welding), MAG and micro plasma arc are carried out by experienced and qualified welders. Stainless steel and ADCAPure weldings are performed in a dedicated contamination free environment to ensure the highest standard.
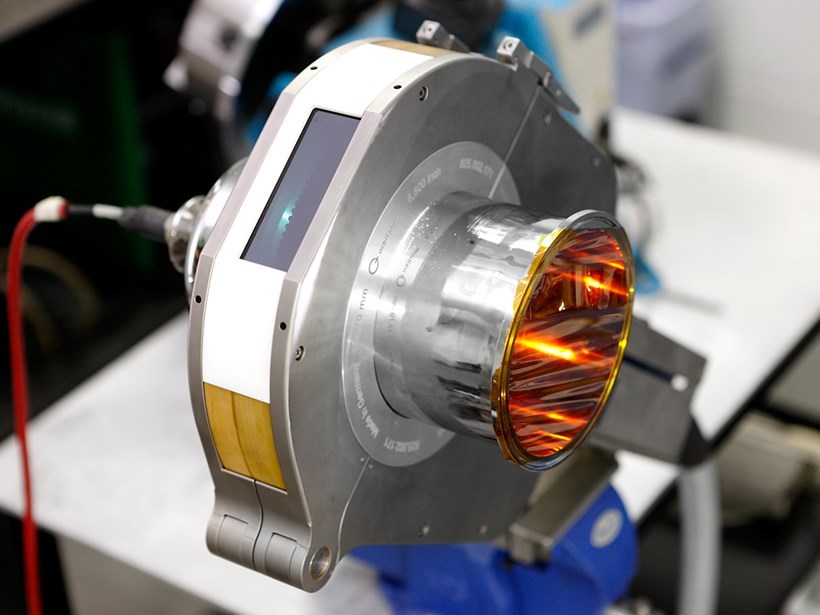
Technology
Welding
Several welding procedures such as orbital, manual and mechanized TIG, MMA (stick welding), MAG and micro plasma arc are carried out by experienced and qualified welders. Stainless steel and ADCAPure weldings are performed in a dedicated contamination free environment to ensure the highest standard.
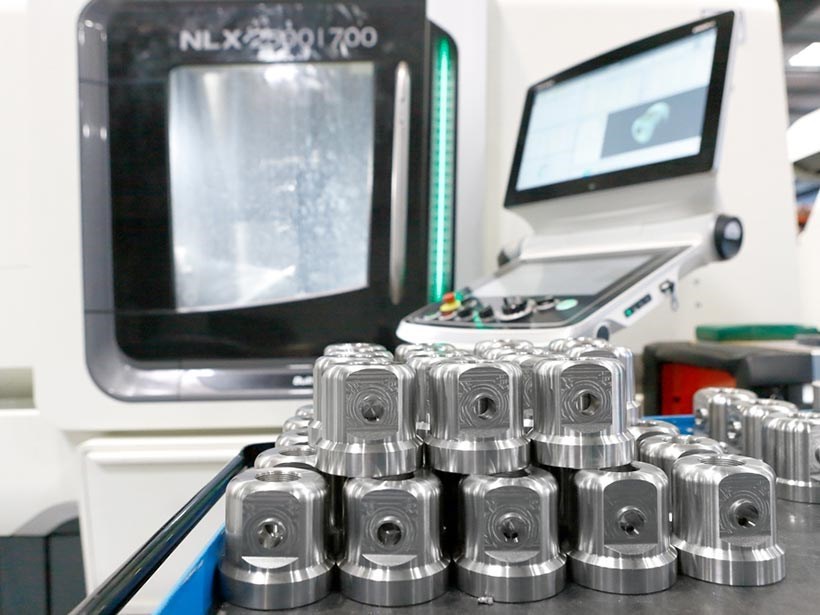
Technology
Machining
The strong investment in state of the art machinery allows us to achieve a high level of quality and reliability, as well as a natural increase in productivity and decrease in delivery times, specially for non-standard series of products.
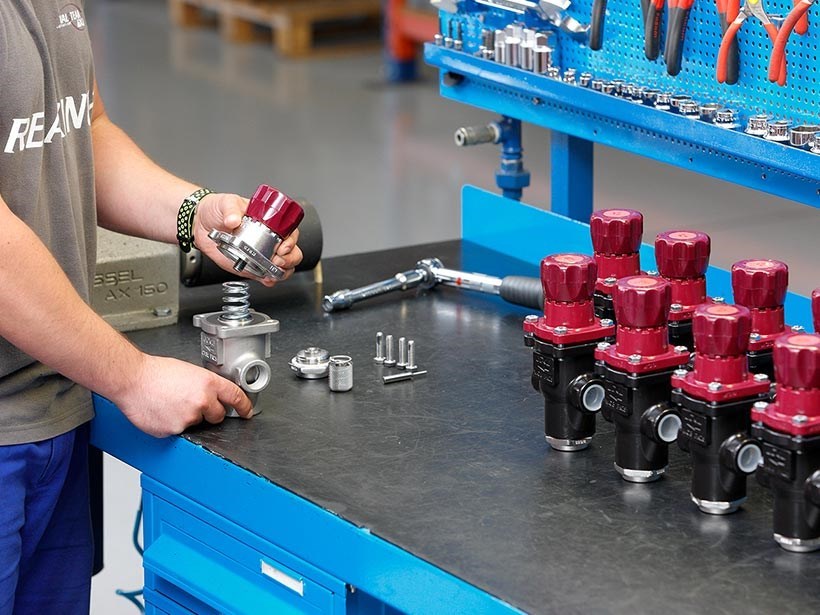
Technology
Assembly
It's the place where we assemble all the components, where craftsmanship and technology come together to obtain the final result. Here ADCA products become ready for battle!
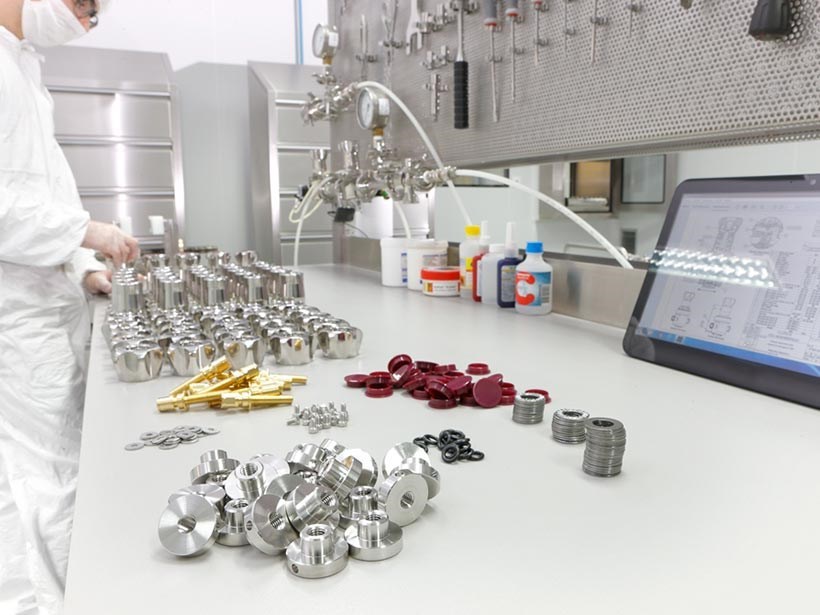
Technology
Assembly
It's the place where we assemble all the components, where craftsmanship and technology come together to obtain the final result. Here ADCA products become ready for battle!
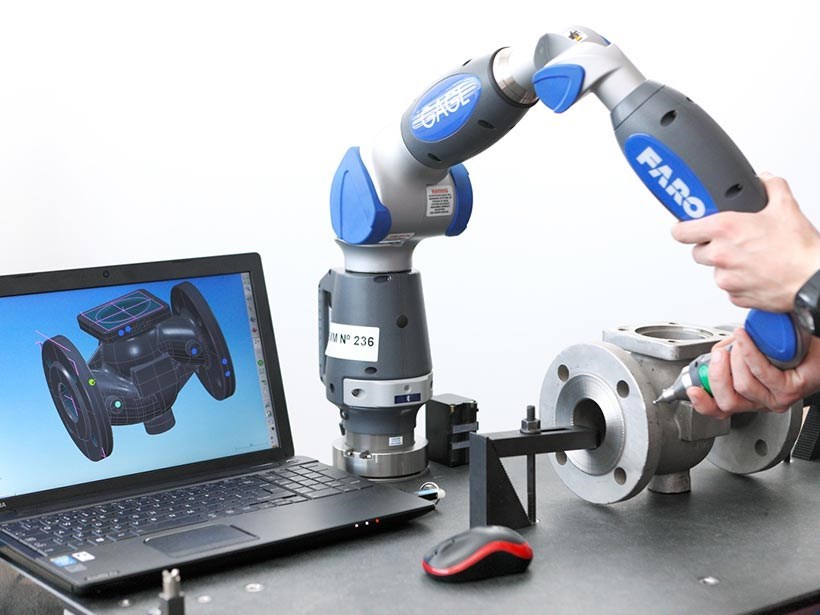
Technology
Quality control & tests
Products are meticulously tested and rigorously controlled throughout the manufacturing process granting the highest level of quality and reliability. From raw material control via spectometry and 3D measuring to final product testing.
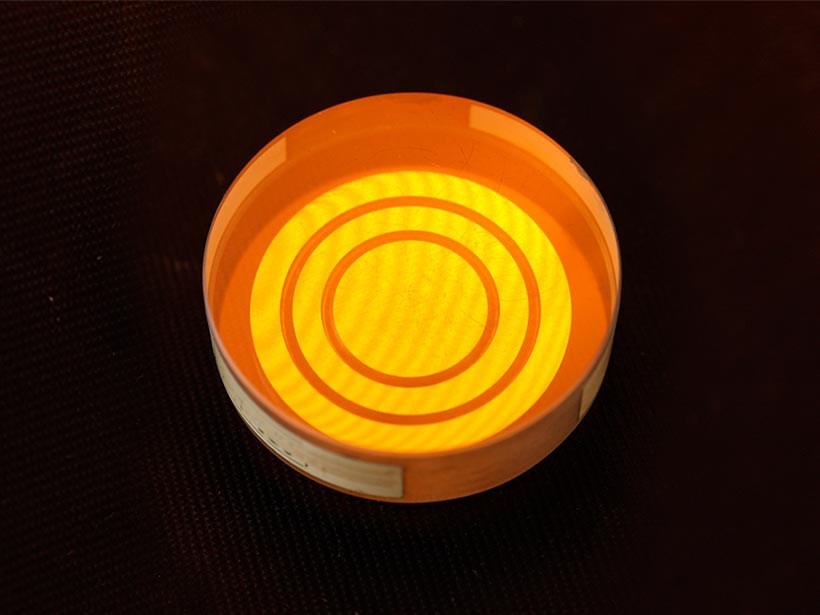
Technology
Finishing
Most of the components used on our products must be submitted to grinding, burnishing, lapping, polishing and other operations. These finishing processes are handled by specialized personnel and controlled by our quality department in our laboratory, supported by the most modern metrology and testing equipment.

Technology
Finishing
Most of the components used on our products must be submitted to grinding, burnishing, lapping, polishing and other operations. These finishing processes are handled by specialized personnel and controlled by our quality department in our laboratory, supported by the most modern metrology and testing equipment.
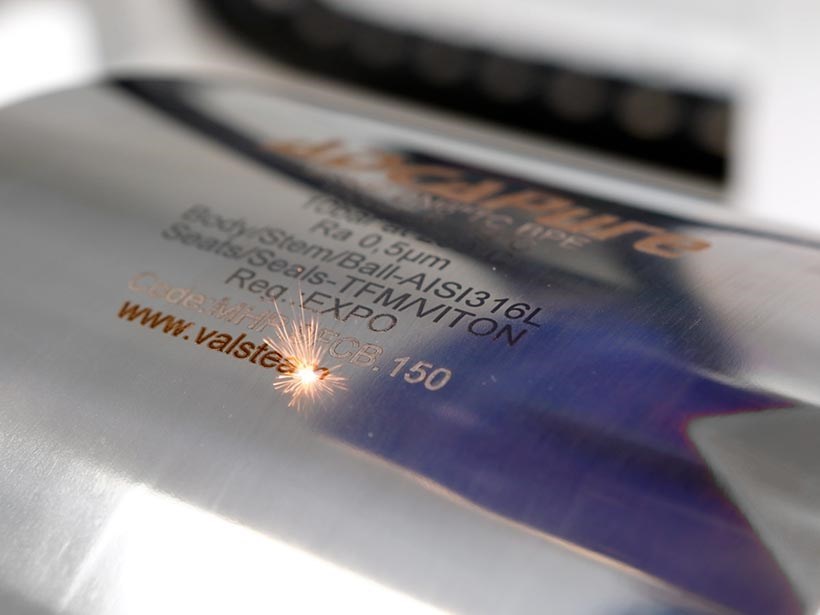
Technology
Marking
Laser marking, tagging, engraving... these are some of the technologies we use on a daily base to carefully identify our products, and guaranty its future traceability.
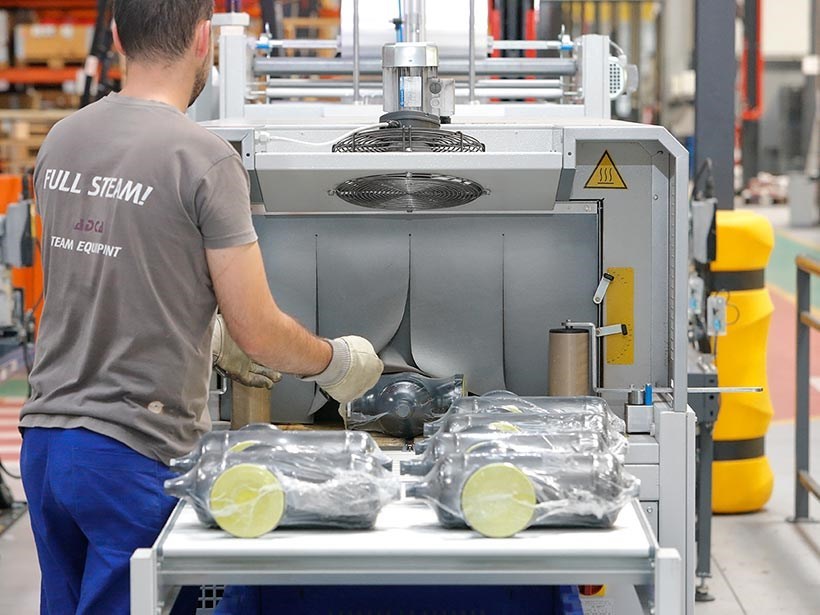
Technology
Packaging
In Valsteam we give our best to properly package our goods, protecting them from damage during transport and storage.
Movies
CONSTRUCTION PHASE I
_
CONSTRUCTION PHASE II
_
CONSTRUCTION PHASE III
_
CONSTRUCTION PHASE IV
_
CLEAN ROOM
_
TEST BENCH & TRAINING FACILITIES
_
FROM PORTUGAL TO THE WORLD
The high-quality standards we put in all our products are recognized worldwide, and today our brand ADCA can be found in over 100 countries and in practically all kinds of industries.